Plant & Process
Digital Twins for Oil and Gas
In the oil and gas industry, digital twin technologies help companies improve operational efficiency, enhance safety, reduce downtime, and lower costs.
Predictive Maintenance of Offshore Platforms
Continuously monitor critical equipment using sensor data to detect anomalies and predict when components will fail. Engineers can schedule maintenance before breakdowns occur.
Remote Operations & Collaboration
Digital twin technologies can real-time connect to monitoring and control assets remotely, reducing the need for personnel to be on-site and thereby reducing risk and improving safety.
Share digital twin views and tools for key personnel and service providers to real-time annotate, comment and collaborate.
Refinery Process
Optimization
A refinery that integrates real-time process data with predictive simulations to optimize refining operations, such as adjusting temperatures, pressures, and flow rates to improve efficiency. Benefits include: higher output, lower energy consumption, and reduced emissions by continuously optimizing refining processes.
Pipeline Integrity and Leak Detection
Digital twins of pipelines can be used to monitor pressure, flow, and temperature in real-time. By detecting anomalies in pipeline conditions, the digital twin can predict and locate potential leaks or failures before they happen.
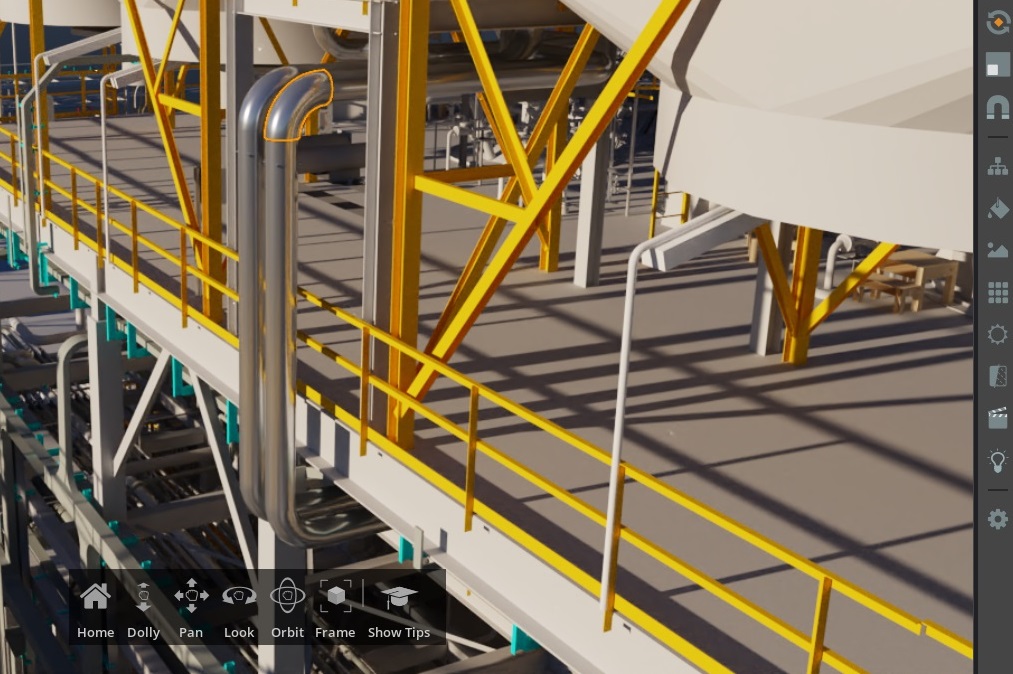
Leverage digital twins to manage operations
Field Management: Digital twins of oil fields integrate data from multiple wells to simulate fluid dynamics, reservoir behavior, and production rates. Engineers can use these insights to optimize well output, manage resources better, and extend field lifespans.
Failure Prevention: By simulating stress on equipment and identifying potential weaknesses, digital twins enable companies to proactively address maintenance needs and avoid costly equipment breakdowns.
Digital Twins in the Chemical Industry
By integrating 3D data, real-time information, predictive analytics, and simulations, digital twins help companies streamline complex chemical processes, reduce downtime, lower costs, and accelerate innovation.
Process Optimization
Digital twins can integrate with industry standard process stimulations to enable engineers to adjust parameters like temperature, pressure, and reaction times and visualize the results
Predictive Maintenance
Monitor the health of critical assets such as reactors, pumps, and heat exchangers.
By collecting real-time data and using predictive analytics, a twin can help forecast equipment failures, allowing for scheduled maintenance before issues occur.
Safety & Risk
Management
Simulate various risk scenarios, such as equipment malfunctions, chemical leaks, or safety protocol failures and use these simulations to help identify potential risks and test emergency responses, ensuring preparedness for real-world situations.
Sustainability & Emissions Reduction
Model the environmental impact of chemical processes and allow companies to test greener alternatives, such as lower-emission production methods or renewable energy integration.
A digital twin can be used to visualize emissions in real-time and provide data to optimize resource use and minimize waste.
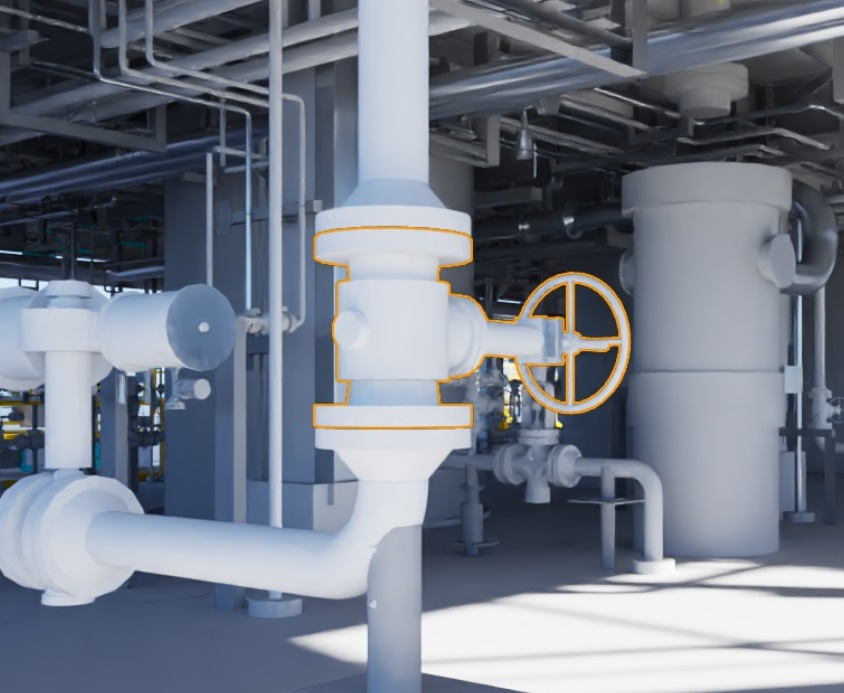
Improve productivity in chemical manufacturing
Inventory and Resource Management: A digital twin of the supply chain can integrate data from raw material suppliers, transportation systems, and storage facilities. This helps companies manage inventory levels, ensure raw materials are delivered on time, and minimize delays in production.
Energy Consumption Monitoring: Digital twins can track energy usage across the entire production process, from heating and cooling to mixing and separation. By visualising energy data, a digital twin can help you identify inefficiencies and suggest process adjustments to reduce energy consumption without compromising productivity.
Digital Twins in Mining
Mining operations involve complex, large-scale processes, often in remote and harsh environments. By integrating real-time data from equipment, geological models, and environmental factors, digital twins can support predictive insights, visualise simulated scenarios, and underpin informed decision-making.
Virtual Training Environment
Digital twin technologies and 3D and geospatial data can provide a safe and efficient training environment that allows experienced personnel to pass on their knowledge to other staff to minimize risks of costly accidents or injuries and increase spatial awareness.
Equipment Maintenance & Reliability
By using a digital twin to monitor the condition of equipment (e.g., trucks, drills, conveyors) in real time, mining companies can apply predictive maintenance. This allows maintenance teams to forecast when equipment will fail and perform repairs before breakdowns occur.
Operational Efficiency & Resource Optimization
Enable real-time tracking of operations, including resource flow, material movement, and energy consumption. A digital twin can help optimize production schedules, minimize energy use, and increase throughput by continuously adjusting based on real-time data.
Safety & Risk
Management
Mining companies can use these digital twin models to simulate emergency scenarios in a risk-free virtual environment.
These simulations provide staff with invaluable experience, helping them understand how to respond effectively and safely in real-world situations.
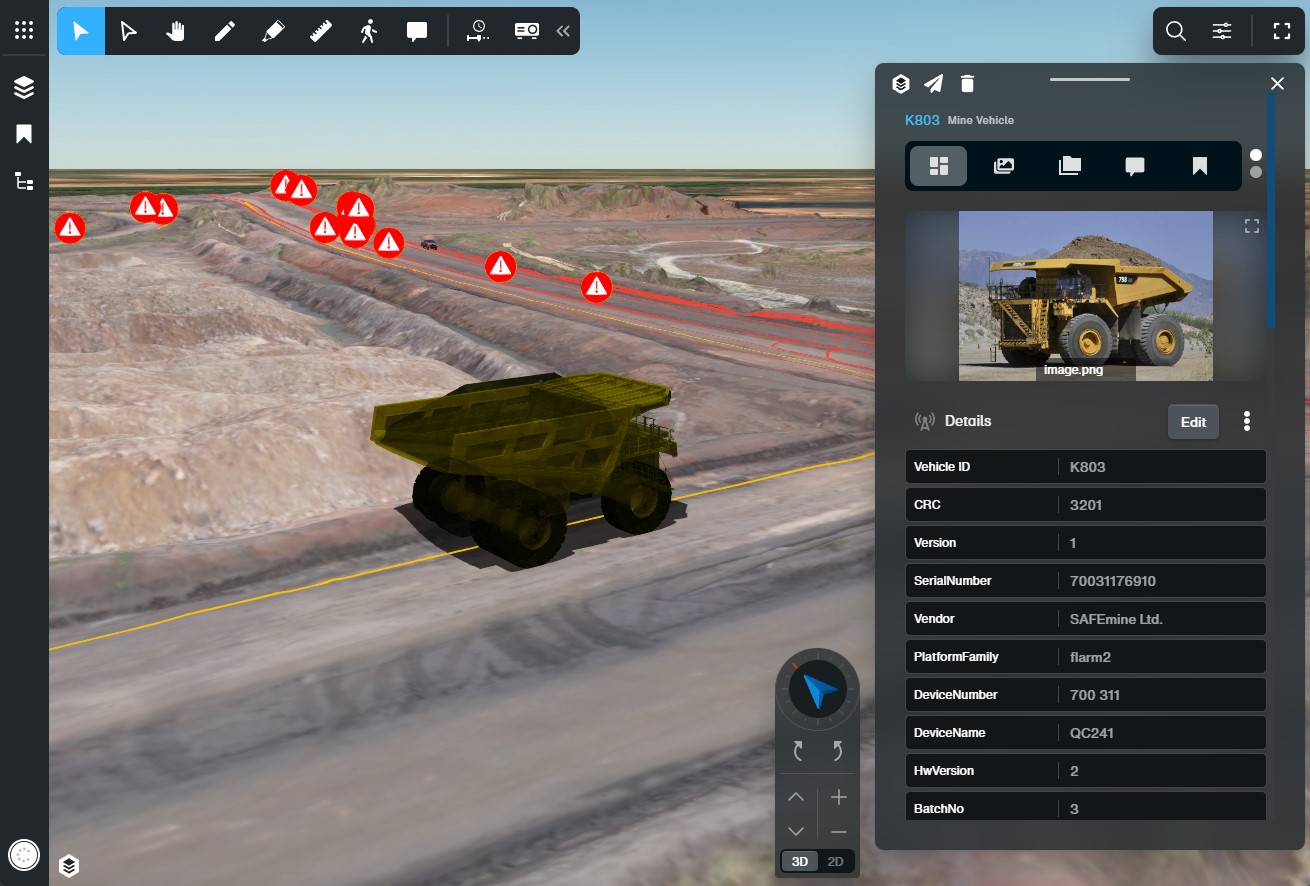
Maximise operational efficiency
Tracking Operational Performance: Provide a real-time view of equipment performance, including productivity rates, equipment health, and load capacities. Tracks how much material is moved by trucks or the efficiency of crushers in processing ore.
Remote Decision Making: Use the digital twin to monitor and control mining activities remotely, making adjustments based on real-time data without the need to be physically present at the mine site.
Industry Use Cases
Companies that love what we’re doing
Companies that love what we’re doing